Nails
Browse all single and collated nails for use with battery-, gas- or powder-actuated fastening tools here
10 Products
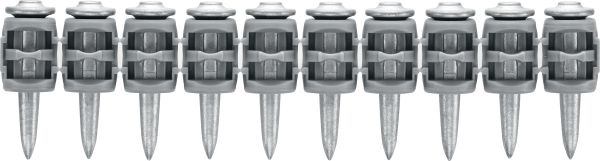
New
- Description
- Collated nails for fastening to concrete and other base materials using the BX 3 cordless nailer
- Base materials
- Concrete (soft), Concrete (tough), Masonry (solid limestone brick), Masonry (grout filled concrete block)
- Minimum thickness of base material (concrete)
- 60 mm
- Corrosion protection
- Galvanised zinc coated <20 µm
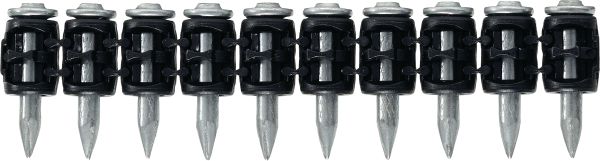
New
- Description
- Collated nails for fastening to concrete and other base materials using the BX 3 cordless nailer
- Base materials
- Concrete (soft), Masonry (solid limestone brick), Masonry (grout filled concrete block)
- Minimum thickness of base material (concrete)
- 60 mm
- Corrosion protection
- Galvanised zinc coated <20 µm
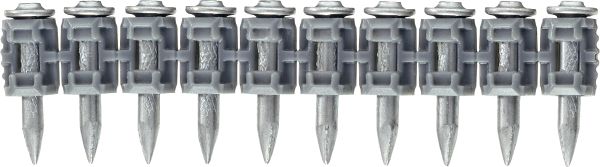
New
- Description
- Collated nails for fastening to concrete and other base materials using the GX 3 gas nailer
- Base materials
- Concrete (soft), Masonry (solid limestone brick), Masonry (grout filled concrete block)
- Minimum thickness of base material (concrete)
- 60 mm
- Corrosion protection
- Galvanised zinc coated <20 µm
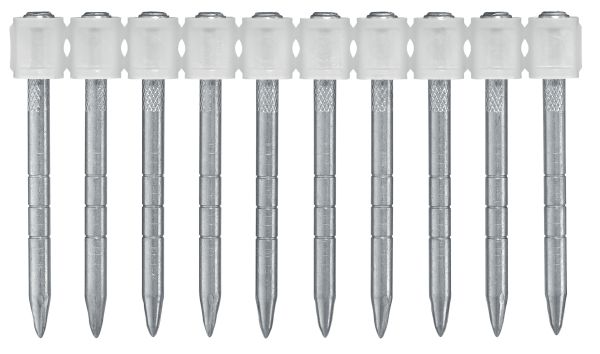
- Description
- Collated nail for temporarily fastening formwork to concrete using powder-actuated nailers
- Base materials
- Concrete (soft), Masonry (solid limestone brick), Steel
- Minimum thickness of base material (concrete)
- 80 mm
- Corrosion protection
- Galvanised zinc coated <20 µm
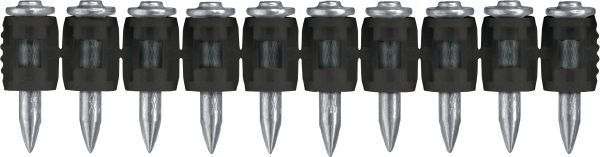
New
- Description
- Collated nail for fastening to concrete using powder-actuated nailers
- Base materials
- Concrete (soft), Masonry (solid limestone brick)
- Minimum thickness of base material (concrete)
- 80 mm
- Corrosion protection
- Galvanised zinc coated <20 µm

- Description
- Single nail for fastening to concrete using powder-actuated nailers
- Base materials
- Concrete (soft), Masonry (solid limestone brick)
- Minimum thickness of base material (concrete)
- 80 mm
- Corrosion protection
- Galvanised zinc coated <20 µm
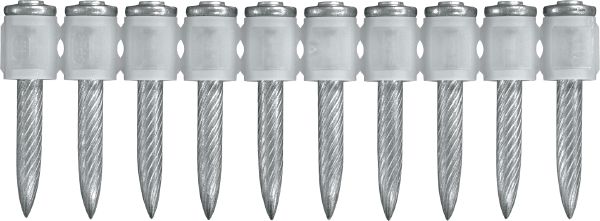
- Description
- Collated nails for fastening to concrete and steel using powder-actuated nailers
- Base materials
- Concrete (soft), Concrete (tough), Steel
- Minimum thickness of base material (concrete)
- 80 mm
- Minimum thickness of base material (steel)
- 6 mm

- Description
- Single nail for fastening to concrete and steel using powder-actuated nailers
- Base materials
- Concrete (soft), Concrete (tough), Steel
- Minimum thickness of base material (concrete)
- 80 mm
- Minimum thickness of base material (steel)
- 6 mm
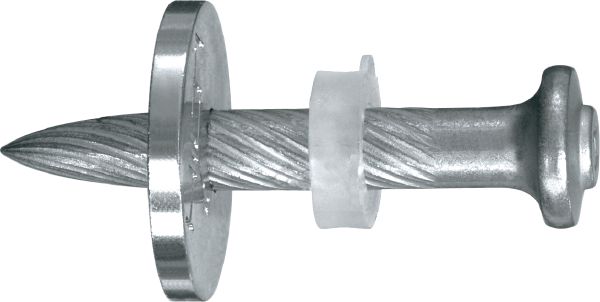
- Description
- Single nail for fastening to concrete and steel using powder-actuated nailers
- Base materials
- Concrete (soft), Concrete (tough), Steel
- Minimum thickness of base material (concrete)
- 80 mm
- Corrosion protection
- Galvanised zinc coated <20 µm
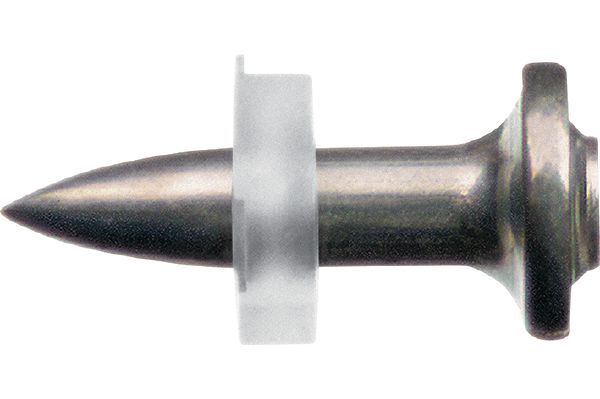
- Description
- Single nail (stainless steel) for fastening to steel using powder-actuated nailers in corrosive environments
- Base materials
- Steel
- Minimum thickness of base material (steel)
- 5 mm
- Corrosion protection
- Stainless steel A4(316) or equivalent

How to choose the right nail
For direct fastening applications from drywall track to metal decking
There’s a large variety of nails to choose from for direct fastening applications. It’s not always easy to understand the differences between the various nail types and to select the right nail for your needs. Here we highlight key things to keep in mind and give you some application examples to help guide your search.

Choosing nails: the basics
Consider application, base material and material being fastened
- Application: For example, interior drywall track, electrical fastening, or permanent fastening to concrete.
- Base material: For example, soft, medium or tough concrete, masonry, wood or steel
- Thickness of material you're fastening: Everything from cable ties to metal sheets.
Other factors include environmental conditions, specific approvals and what material the nail is made of. With this in mind, you need to consider what load will be applied, stick rate (percentage of nails that hold firmly) and price.

Nail selection 1: applications
Specific task requirements are critical for nail choice
Do you need solutions for light-duty applications like fastening cables and conduits? Or are you doing heavy-duty work like fastening metal decks? What are the load requirements for each fastening point?
Your answers here can determine the system and nails you use. For example ligher duty applications can be done with gas (GX) and battery (BX) - for heavier duty you may only be able to use powder-actuated (PAT) tools.

Nail selection part 2: base material
Understand your base material to help ensure lowest setting failure
For fastening to concrete, the strength of concrete (soft or tough) is key. We have different nail classes here. All classes perform similarly in soft concrete but as concrete get tougher, the stick rate varies. With tougher concrete, premium nails perform better than cheaper counterparts.
For fastening to steel, nail choice depends on steel grade and thickness. You may also need more than one type of nail for your project.

Nail selection part 3: material being fastened
Consider material thickness and recommended embedment depth
To get the right length nail for your application, you need to look at the thickness of the material being fastenend and the recommended nail embedment for your base material.
Thickness of material and load requirements may also determine the technology you can use. For various applications, you may have options at different price points. Need more information? See the technical data on specific nail product pages or see our Direct Fastening Technology Manual.
Nail selection: sample applications
Interior drywall track
Application
Light-duty (thin steel sheet to concrete or steel). Recommended technology: BX (battery nailer) with collated nails for most productive fastening
Base material
Tough concrete (greater than 40 MPa)
Fastened material thickness
Track thickness is 0.9mm, no intermediate layers. As we have an 18mm embedment requirement in concrete, we select the 20mm long X-P MX.
Cost-competitive solution
X-C B3 MX can also be used with certain compromise on performance
Exterior track to concrete
Application
16-gauge drywall track to concrete. Recommended technology: Powder-actuated (DX) as high tool energy required
Base material
As perimeter wall is structural application, highest possible fastening quality is required. Best performing option is X-U nail
Fastened material thickness
Usually requires 32mm or 38mm (when fastening in seismically active regions) embedment depth: choose X-U 34 or X-U 40 nails
Cost-competitive solution
No alternative as fastening quality cannot be compromised
Permanent wood to steel attachment
Application
2"x4" (38mm x 90mm) wood pieces to steel for residential house framing. Recommended technology: Powder-actuated (DX) as this is a medium-duty
application
Base material
Carbon steel is used in residential framing, so the only suitable powder driven nail here is X-U
Fastened material thickness
With 38mm wood attached to steel and recomended embedment for powder actuated nails at 12mm, recommended nail length is 50mm. Select X-U 52 MX
Cost-competitive solution
There is no cost-competitive solution for fastening to steel avilable in our portfolio.
Electrical fastenings
Application
Light-duty application not requiring high loads. Recommended technology: BX (battery nailer)
Base material
Cable fastening is usually done on ceilings, so large aggregates in the slab will be closer to ceiling surface. To avoid spalling and ensure highest fastening quality, use X-P nails
Fastened material thickness
Plastic and metal electrical fasteners usually have a hole for the fastening element. Here we need to use a 20mm nail, but it there is a big stand-off, this can be shortened to 17mm. If there is too much spalling of concrete – we recommend increasing nail length to X-P 20 or X-P 24, to improve fastening quality.
Cost-competitive solution
X-C B3 MX can be used with certain compromise on stick rate
Temporary wood to concrete
Application
Recommended technology: Powder-actuated (DX) as high tool energy required
Base material
Fastening of formstops and temporary barriers usually done to fresh concrete, so standard X-C fasteners should provide good stick rate
Fastened material thickness
To attach a 20mm wood piece you need to ensure minimum 22mm nail embedment in concrete – so you need to have a nail longer than 42 mm. X-C 42 is the right choice.
Alternative solution
If concrete is not as fresh and you are looking for ways to improve stick rate, try our premium X-U nail.
Metal roof decking
Application
Careful selection of nails is particularly important for fastening of metal deck over the roof of steel-based buildings. The nails need enough load bearing capacity to withstand the weight of the deck when subject to wind, snow and other types of loads. This is especially true with diaphragm design.
Base material
Key factors are thickness and steel grade of the structure we are planning to attach the deck to. Is it a 6 mm bar joist or 12 mm I beam? If it is a bar joist our best performing solution is X-HSN 24.
Fastened material thickness
Since we only have X-HSN in one length we need to make sure that we respect the maximum allowed fastened material thickness.
Cost-competitive solution
For such a critical application, you need maximum nail performance: the X-HSN 24.
Legal note: All applications and calculations listed above are intended as a guide only. The final choice of nail is the customer's decision and strict adherance to operating instructions and other technical data supplied by Hilti during nail installation is required.
Why choose Hilti nails for direct fastening?

Up to 5 times faster
When combined with our direct fastening tools, our nails can help you be more productive than with traditional time consuming methods such as drilling and anchoring, or welding, clamping and bolting.

Tackle multiple applications
Our nails can be used with three direct fastening technologies, providing the right amount of energy to suit most applications, from fastening drywall track to framing or formwork, all in one cordless tool.

More safety on the jobsite
Fasten more quickly and safely on a wide range of surfaces, even tough concrete or high-strength steel. No drilling reduces the dust and noise onsite, plus our cordless systems mean no cables to trip over.

Nails for your project needs
With our color-coded multiline approach, you can easily choose from Standard, Premium or Ultimate options depending on your project needs.