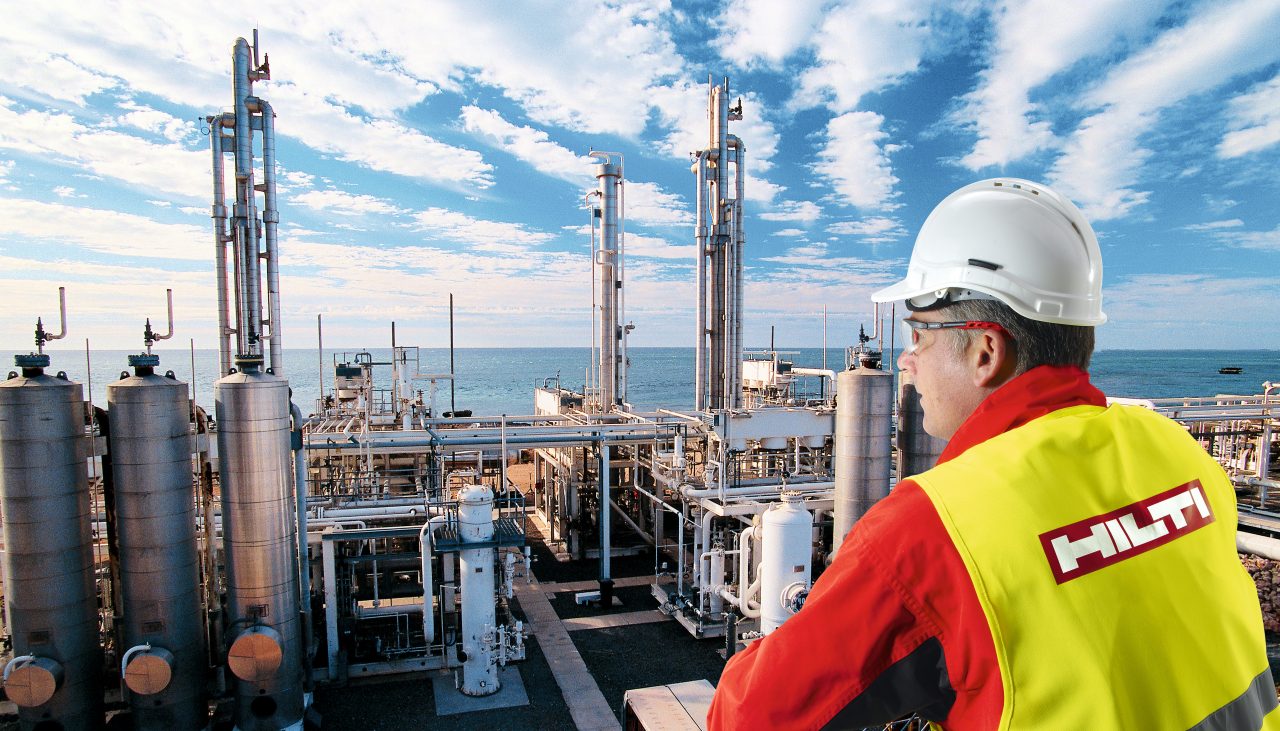
Corrosion in Construction
Why it's important to consider corrosion on your jobsite
It takes roughly one fifth of the world’s annual steel production to replace parts damaged by corrosion. While all these repairs add up to a considerable economic loss, a greater concern is the safety risks, where corrosion may lead to failure in fastening a system.
Corrosion protection is the best way to help mitigate these risks.
Active corrosion protection includes measures that directly influence how steel reacts to its corrosive environment, e.g. galvanic separation, resistant materials, or cathodic protection.
Passive corrosion protection decelerates corrosion through the isolation of the metal material from the corrosive agent by the application of metallic or non-metallic protective coatings.
Why is corrosion relevant?
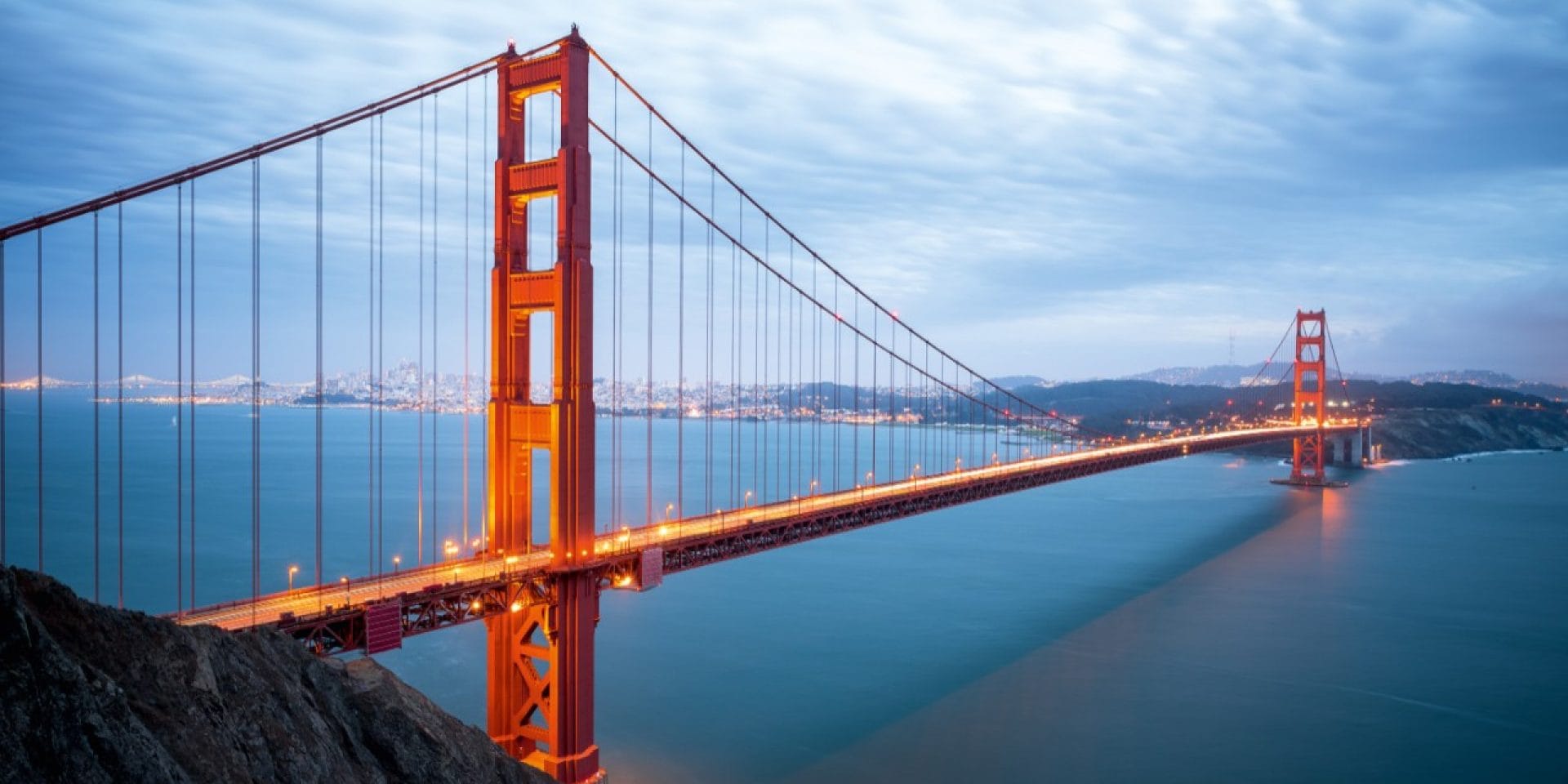
According to estimates by the American Galvanizers Association, if the Golden Gate Bridge had been completely hot-dip galvanized – although it would have added approximately 15% to the construction costs – it would have saved up to $1billion in maintenance and repair, since the opening of the bridge.
This is an extreme example but investing in effective corrosion protection from the start can pay off in the long run.
As an alternative to relying on future inspections or maintenance to ward off corrosion, proper corrosion resistance can be incorporated during the design stage.
Ineffective corrosion protection not only shortens a structure's lifetime but (in the worst cases) can also lead to expensive rework or possible failures.
Source: https://galvanizeit.org/about-aga/news/article/how-much-money-if-the-golden-gate-bridge-had-been-galvanized
What is corrosion?
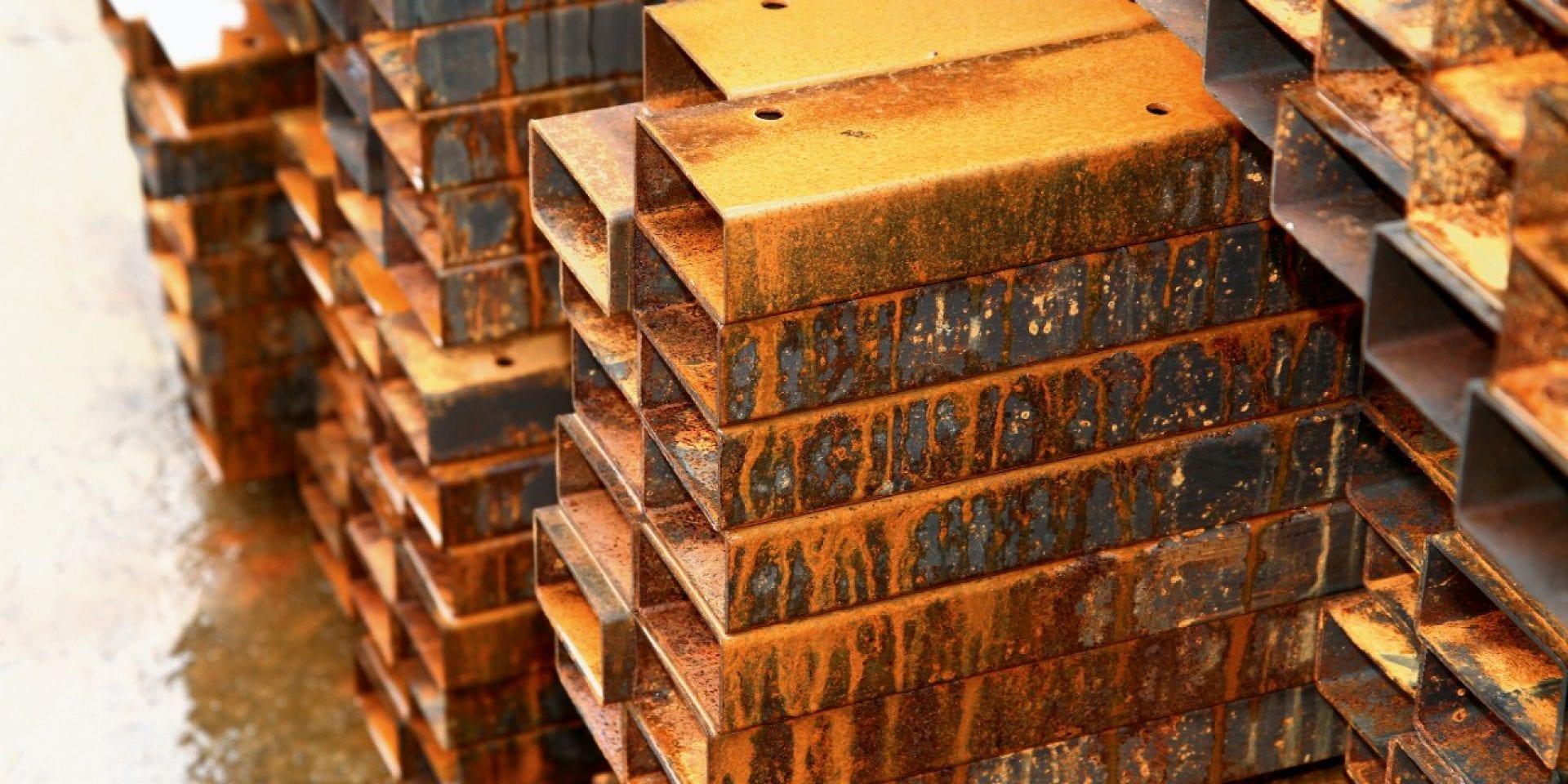
Corrosion is the physicochemical interaction between a metal and its environment, which results in changes in the metal’s properties and may lead to significant functional impairment of the metal, the environment, or the technical system of which they form a part (see ISO 8044:2010).
With the metals commonly used in engineering – such as carbon steel, stainless steel, zinc, copper and aluminum – typical corrosion is the degradation over time to its more stable (pre-manufactured) state.
Influencing factors
To evaluate the risk of corrosion, it is essential to assess the interaction between environmental conditions, material properties, material combinations and design characteristics. Following are the most common influencing factors which need to be considered (note there are numerous other less common factors associated with specific applications and environments):
- An Electrolyte: a requirement for all atmospheric corrosion reactions (e.g. humidity, moisture, etc.)
- Temperature: the higher the temperature, the higher the rate of corrosive attack
- Chemicals: such as salt in sea air or used for de-icing in winter or chlorine in swimming pools, etc. can accelerate corrosion
- Industrial pollution: sulphur dioxide and other pollutants can accelerate corrosion
- Dissimilar metals: the direct contact of dissimilar metals (where one metal is less noble than the other) increases corrosion risk
Types of corrosion
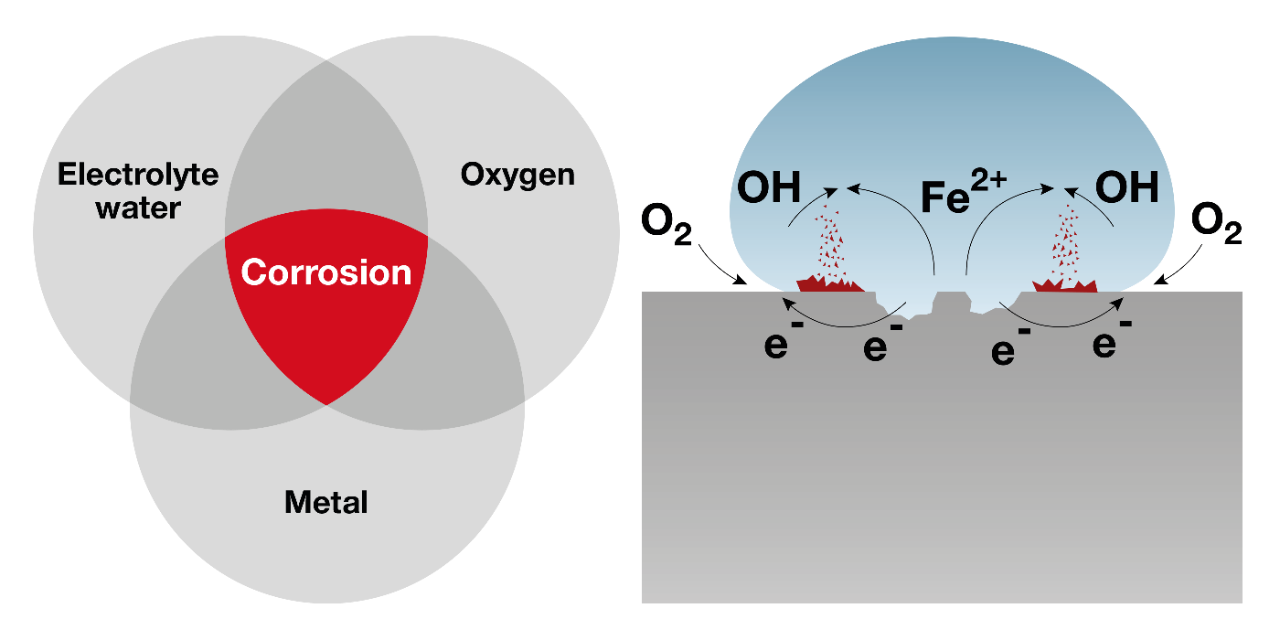
Electrochemical reaction
The most common corrosion reaction is electrochemical in nature. Such reactions imply an electrical exchange by way of electrons in the metal and ions in a conducting electrolyte, such as water.
Examples of this type of corrosion are:
- Uniform corrosion
- Crevice corrosion
- Pitting corrosion
- Galvanic corrosion
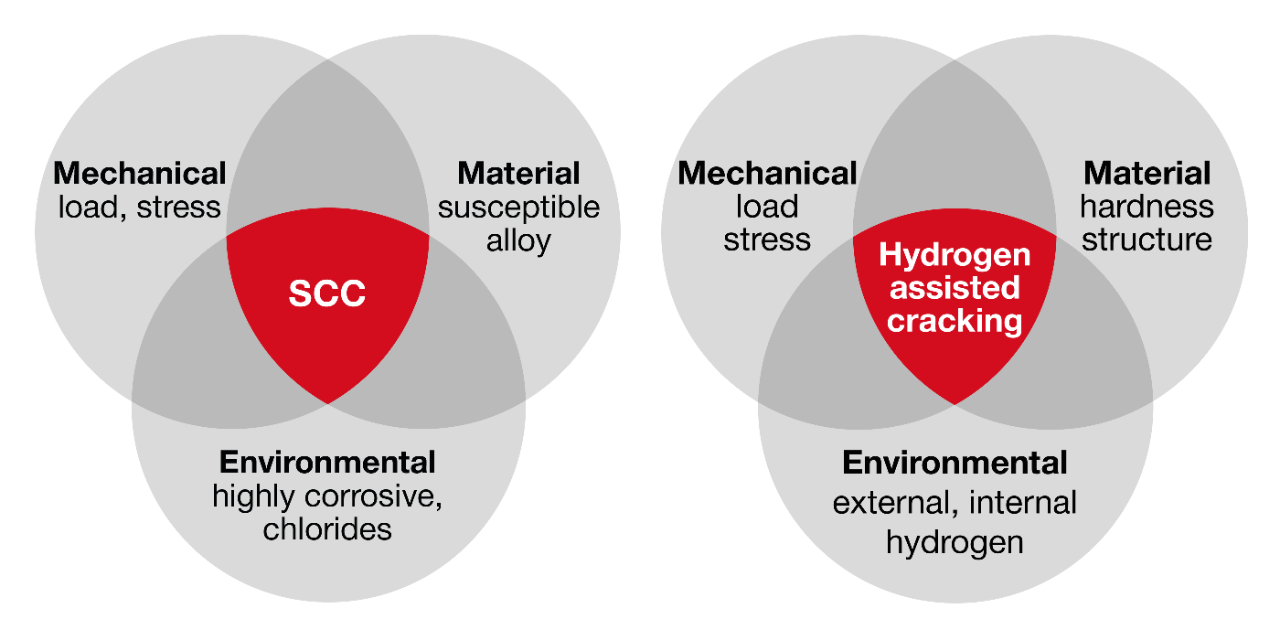
Combined influence of mechanical stresses
This type of corrosion is a combined mechanical and electrochemical corrosion process that results in cracking of certain materials. Internal stresses in a material can be sufficient to initiate the attack.
This is the process by which high-strength or hardened carbon steel under stress becomes brittle and suddenly fails.
Depending on your application, this form of corrosion restricts the use of certain materials.
Examples of this type of corrosion are:
- Stress corrosion cracking (SCC)
- Hydrogen assisted cracking (or secondary hydrogen embrittlement)
Environmental categories
Corrosion in construction has a big impact on costs and safety, and special applications demand special attention to mitigate corrosion risk. An important aspect to consider is the environmental categories.
These are typically categorized by the general corrosivity of the environment, taking into account the common influencing factors discussed above.
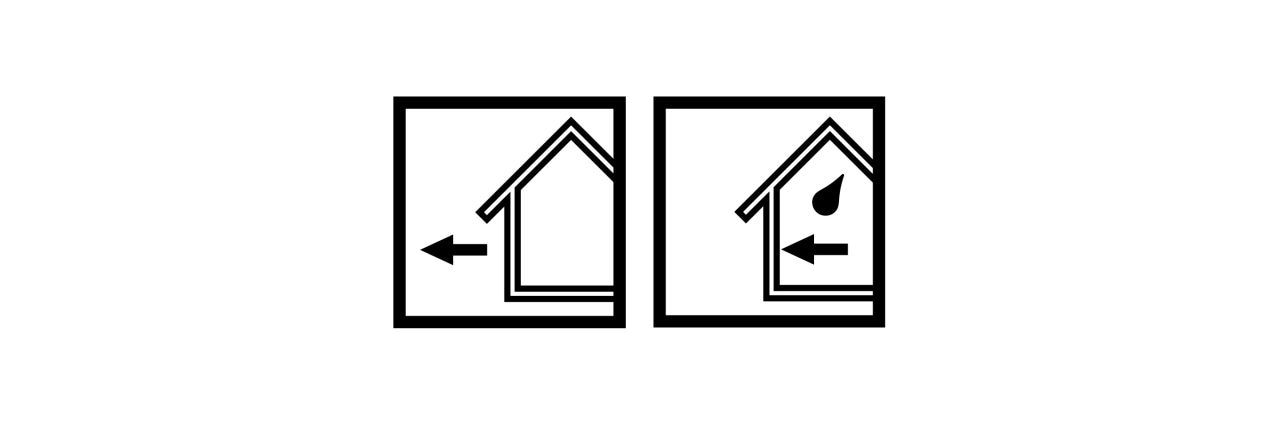
Indoor applications
- Dry indoor environments (heated or air-conditioned areas) without condensation e.g. office buildings, schools
- Indoor environments with temporary condensation (unheated areas without pollutants), e.g. storage sheds
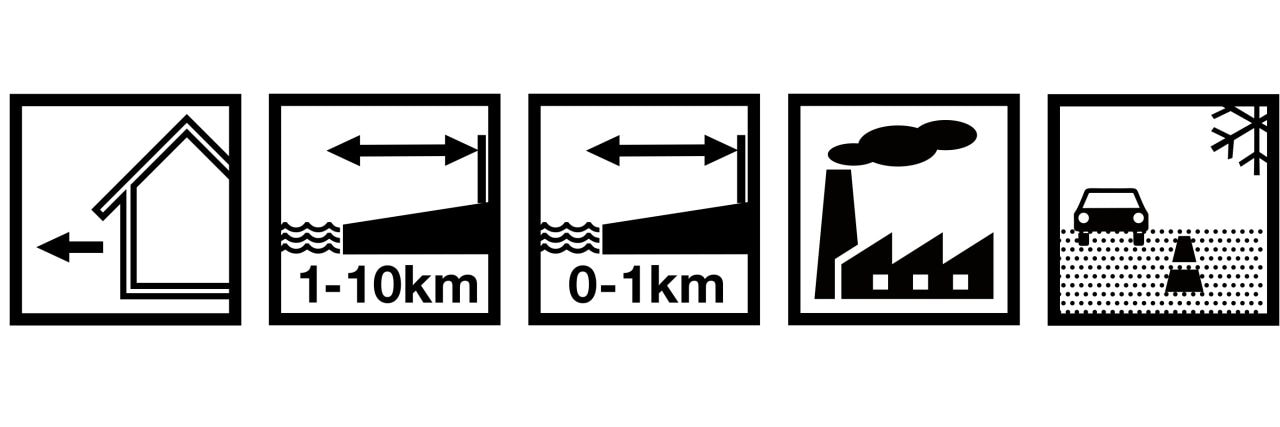
Outdoor applications
- Outdoor, rural or urban environment with low pollution. Large distance (> 10 km) from the sea
- Outdoor, rural or urban environment with moderate concentration of pollutants and/or salt from sea water. Distance from the sea 1-10 km
- Coastal areas. Distance from the sea < 1 km
- Outdoor, areas with heavy industrial pollution. Atmospheric SO2 concentration > 10 μg/m3 as yearly average (e.g. close to polluting plants)
- Close proximity to roadways treated with de-icing salts. Distance from roadways < 10 m
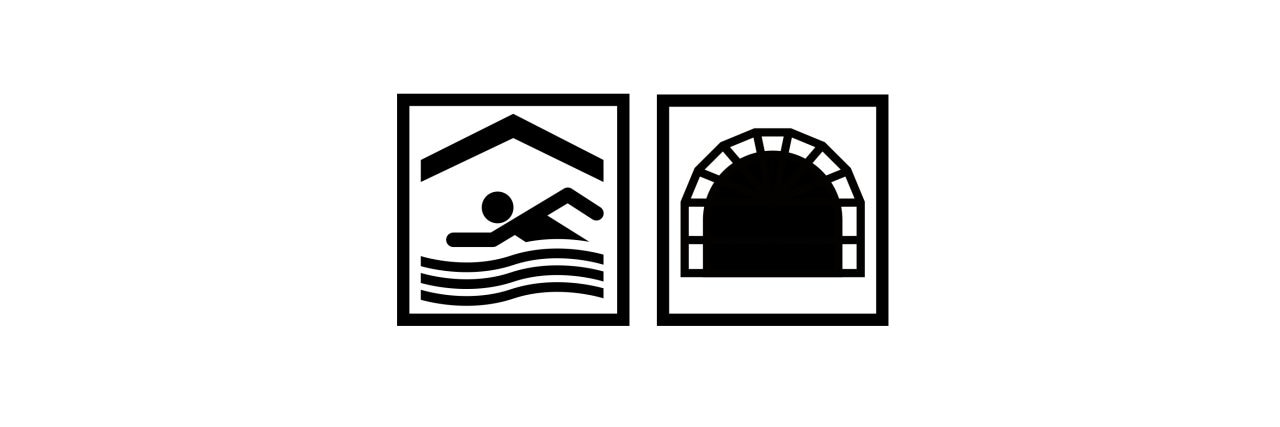
Special applications
Areas with special corrosive conditions, e.g. road tunnels with de-icing salt, indoor swimming pools, special applications in the chemical industry (exceptions possible).
How can I prevent corrosion?
You can’t. Instead, the aim of corrosion protection is to maintain the structural integrity (and in some cases the appearance), for the expected service life of the product or assembly. Passive protection involves selection of a material and/or protective coating suitable for the environmental conditions.
Selecting the right corrosion protection
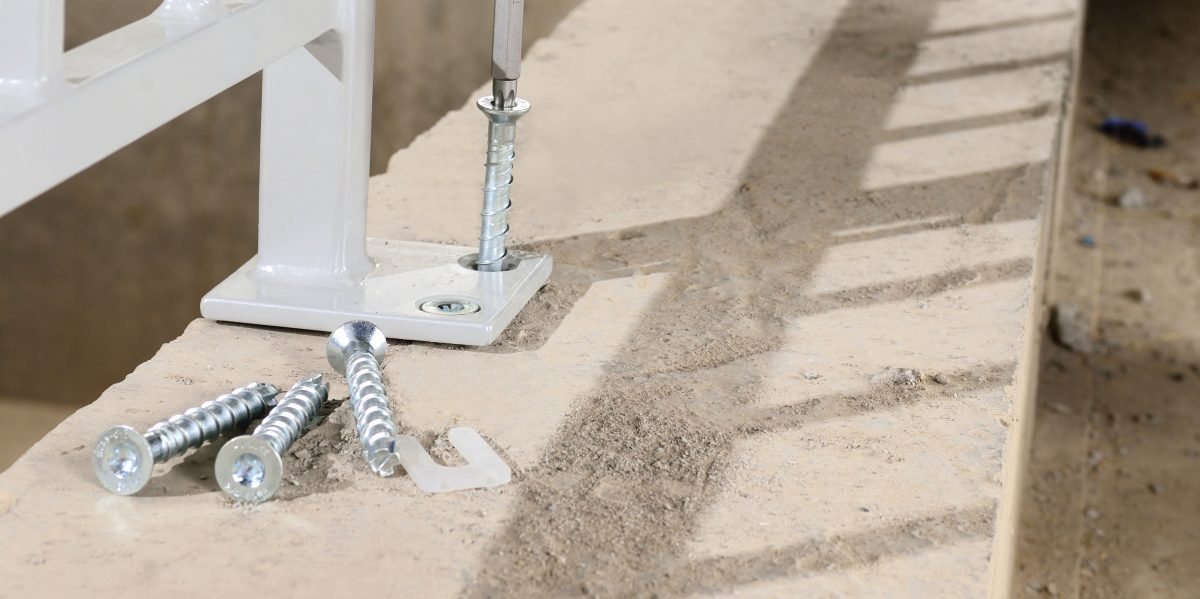
Anchors, powder-actuated fasteners and screws
To increase the performance and reliability of fasteners for their entire service life, all the influencing factors must be identified before a suitable fastener can be selected.
Click the link for a table (on page 5) that provides a general guideline for the most common applications for fastening elements.
View table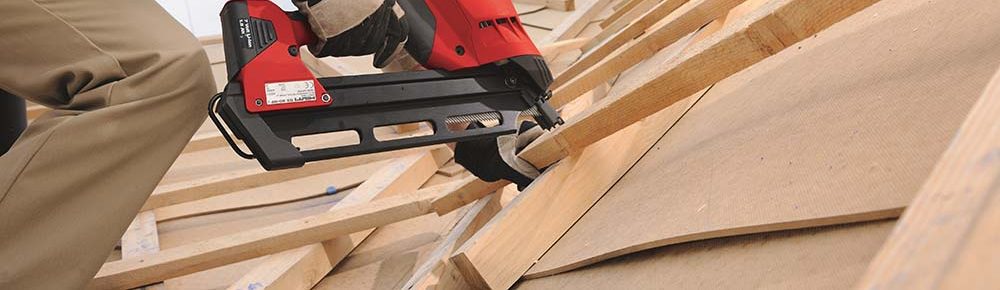
Wood nails
Wood can be corrosive due to the organic acids it contains, or added chemicals (e.g., preservatives or fire retardants). Besides atmospheric conditions, corrosive attack by the wood itself must also be considered when selecting the type of corrosion protection for wood nails.
Click the link for a table (on page 6) that provides a general guideline for common applications in which wood nails are used.
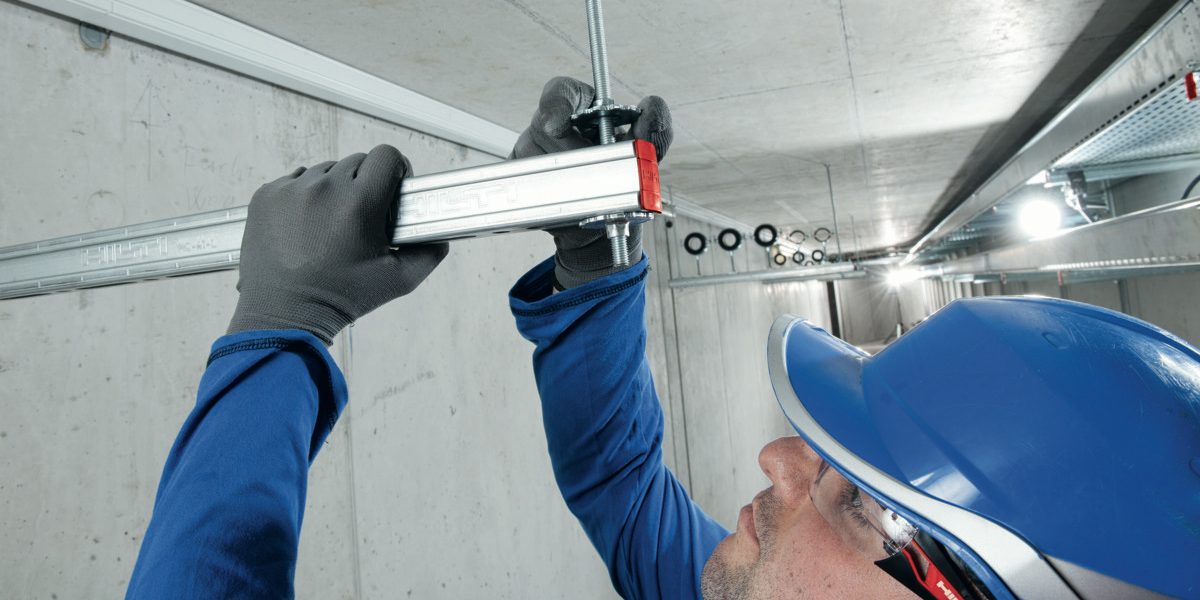
Modular support systems
The typical lifetime rating of initial coatings depends on the corrosiveness of the atmosphere, which differs significantly throughout the world. For a practical approach, Hilti differentiates between the zones.
Click the link for a table (page 7) that provides a general guideline on the typical lifetime expectancy of Hilti installation systems (e.g. channel systems and pipe fastenings).
View tableWhy Hilti is the choice for corrosion protection
Tried and tested
Hilti conducts comprehensive laboratory and field corrosion tests to assess the corrosion protection of its products. Hilti can offer the right solutions with the suitable corrosion protection for a wide variety of environmental conditions.
Whatever your situation, whatever the corrosion resistance you need, Hilti has a solution for you.
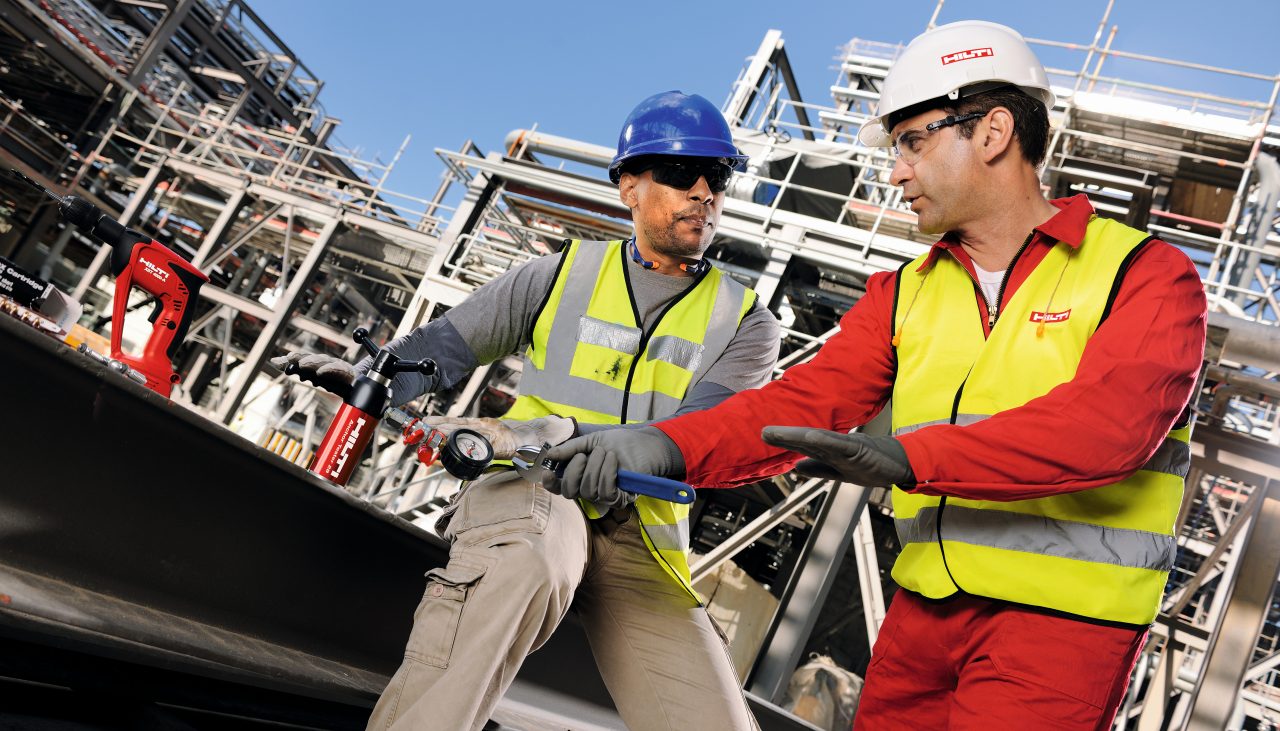
Working together
From design to installation
The Hilti Group has over 28,000 employees in over 120 countries around the world. Local teams of highly trained Account Managers, Field Engineers and office-based teams are available to help you with all aspects of design, logistics and installation. We can be with you on-site, on the phone or on email, wherever and whenever you need us.
We also have a range of digital resources – from PROFIS Engineering software, mobile apps and a comprehensive BIM/CAD library – to help you make the right choice for your project.
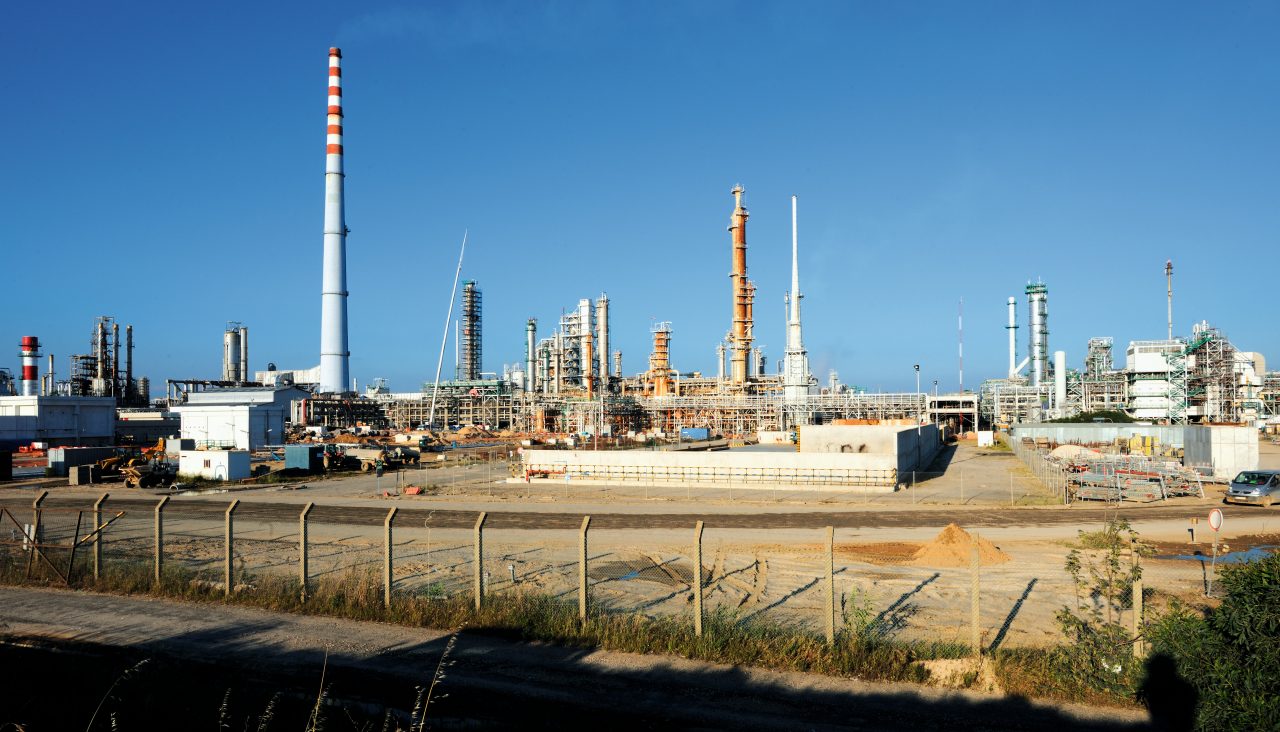
Fastening on steel in corrosive environments
Hilti provides a range of faster, more reliable and efficient solutions for fastening to steel in virtually any corrosive environment, commonly encountered in the energy and industry sector.